The potential and current limitations of Vacuum
Insulation Glazing (VIG)
The insulation performance of windows has dramatically increased
during the last fifty years. The U-value of a state-of-the-art
triple glazing unit is around 0.7 W/(m2·K), which is
still higher than that of a well-insulated wall, with U-values as
low as 0.15 W/(m2·K).
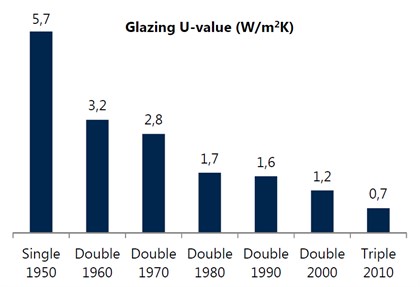
Historical evolution of glazing performance. For comparison,
a well-insulated wall has a U-value of 0.15
W/(m2·K).
Vacuum Insulation Glazing (VIG) have potential U-values lower
than 0.3 W/(m2·K), but currently available products do
not even approach these values due to technical limitations. One of
the most critical aspects of VIG is the edge seal. For typical
products, the edge between both panes is sealed by a
PbO-SiO2 based solder glass before evacuation and
sealing of a pump-out hole. The result is a rigid edge seal and a
visible pump-out hole in one of the corners of the glazing. The
rigidity of the edge seal imposes limitations on the performance of
the VIG unit: for large sizes of highly insulating glazing, large
temperature differences between the inner and outer pane result in
differential expansion of the panes, which may bend and break the
VIG.
The Winsmart VIG
The Winsmart strategy overcomes these problems by using a
flexible edge seal that consists of laser-welded metallic ribbons.
In a first step, metallic ribbons are soldered onto both glass
panes under atmospheric pressure. In the second step, the VIG is
created by laser-welding the metallic ribbons inside a vacuum
chamber. The result is a VIG unit with a flexible edge seal and
without a pump-out hole.
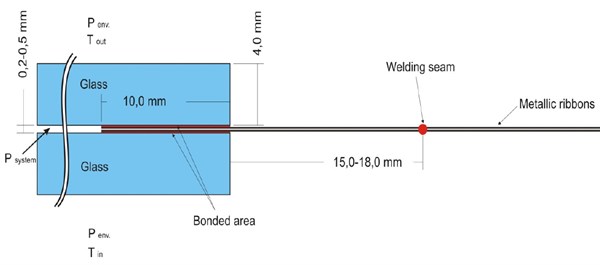
Schematic cross-section of the Winsmart edge-sealing
technology.
Glass-to-metal bonding by liquid solder anodic
bonding
The bonding of metal to glass is notoriously difficult and often
requires metallization of the glass surface before bonding. The
ALTSAB process combines anodic bonding with the use of an
activated liquid tin solder to produce strong hermetic seals. The
liquid solder can accommodate surface roughness and negates the
need for surface pre-treatment or the application of high
mechanical force during the bonding process.
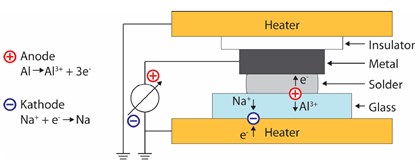
Schematic illustration of the ALTSAB process (Figure from
Elrefaey et al. 2014). The application of a high electric field
(500-1000 V) oxidizes the activating element in the solder (Al)
near the glass-solder interface, dramatically improving bond
strength and the wetting of the glass with liquid thin. At the same
time, the metal-solder bond is forms by soft soldering.
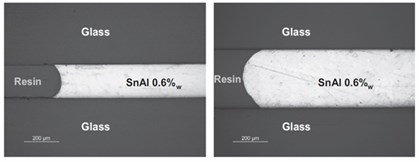
The application of a high voltage (left) dramatically
improves the wetting of the glass by the solder (Figure from
Koebel et al. 2011).
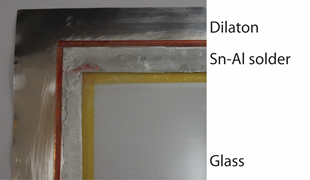
Early glass-to-metal bonding prototype.
Laser welding of metallic ribbons under
vacuum
After bonding the metallic ribbons, a pair of glass panes is
transferred to a vacuum chamber (P < 1E-5 mbar). The spacers
have to be placed before in a way that they don't influence the
optical characteristic of a window. In the vacuum tunnel a plasma
cleaning process is applied to avoid excessive degassing of the
final VIG unit. Then, the top pane is lowered onto the spacers
positioned on the bottom pane and the metallic ribbons are clamped
together. Finally, the metallic ribbons are laser-welded to form a
hermetic seal, while the laser itself is outside of the vacuum
chamber.

Vacuum chamber with laser-welding equipment for 1m x 1m
glass panes.
The advantage of this method is the hermetic sealing without
pumping the VIG afterwards. The joint glass panes leave the vacuum
chamber as a complete VIG.
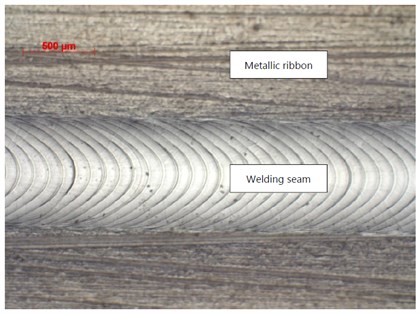
Close-up (top-view) of the laser-welded edge seal. The high
degree of overlap ensures a hermetic seal.
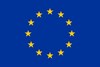
This project has received funding from the European
Union Seventh Framework Programme (FP7/2007-2013) under grant
agreement n° 314407.